Screw air compressors have dramatically transformed industrial compressed air systems, offering superior energy-efficient performance, reliable free air delivery, and flexibility across a wide range of applications. These compressors have evolved significantly, from the decline of piston compressors to the rise of rotary screw air compressors powered by innovations like variable speed drives and oil-free technology. The development of these technologies has redefined productivity, making it essential to understand the differences in maintenance requirements between oil-injected and oil-free screw compressors. This blog explores the development history of screw compressors and offers a detailed comparison of the maintenance practices for both technologies.
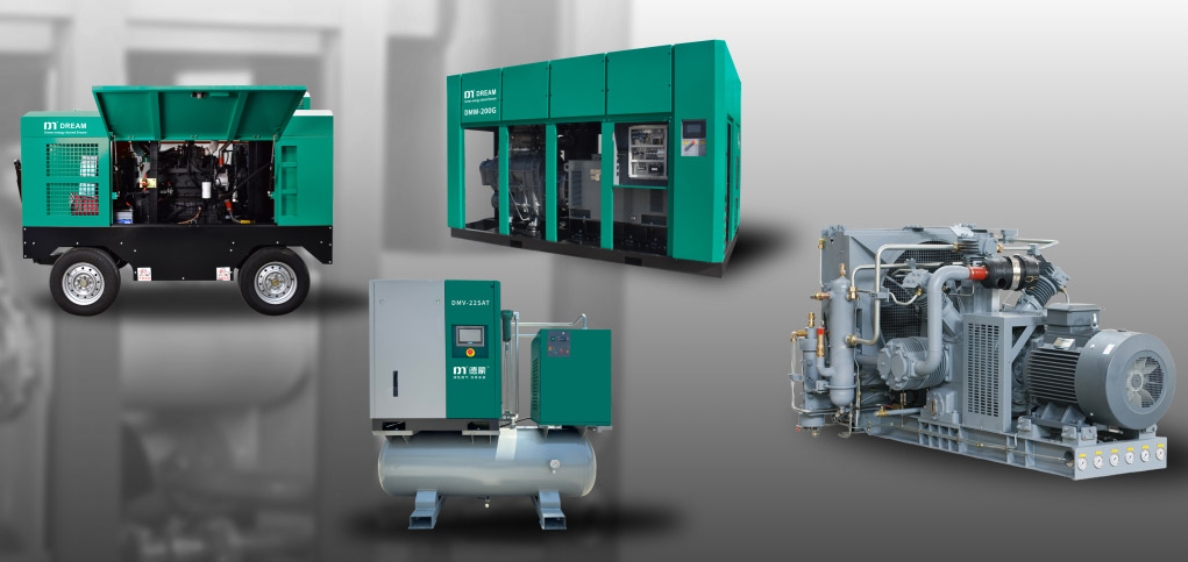
The Development History of Screw Air Compressors: From Positive Displacement to Energy-Saving Innovations
The roots of screw air compressors trace back to the 1930s when Swedish engineer Alf Lysholm pioneered the positive displacement twin-screw design. Initially, this technology was utilized in gas turbines, but it wasn’t until the 1960s that screw compressors gained widespread industrial adoption. This was largely due to advancements in electric motor technology and precision manufacturing, which allowed the compressors to achieve more consistent airflow and quieter operation compared to their piston-driven counterparts.
Key Milestones:
- 1970s: The introduction of oil-injected screw compressors brought oil into the system for lubrication, internal sealing, and cooling. This significantly improved efficiency and reduced wear, making them suitable for high-duty cycles.
- 1990s: The emergence of oil-free screw compressors was a breakthrough, as they eliminated the risk of oil carryover in sensitive applications like food processing and pharmaceuticals. This was achieved through advanced coatings and tight rotor tolerances, ensuring compliance with ISO 8573-1 Class 0 standards.
- 2000s–Present: The integration of variable speed drives (VSD) and permanent magnet motors optimized energy savings. Moreover, modular designs made screw compressors adaptable for a wide variety of industrial applications, from small workshops to large manufacturing plants.
Oil-Injected vs. Oil-Free Screw Compressors: A Maintenance Comparison
While oil-injected screw compressors are ideal for general industrial use, oil-free screw compressors are critical in industries requiring clean, contaminant-free air. Both types offer distinct benefits, but they also come with their own maintenance demands. Let’s break down the key maintenance considerations for each:
Core Features:
- These compressors use oil-lubricated systems for sealing, cooling, and noise reduction.
- Suitable for both fixed-speed and variable-speed operations, making them ideal for high-duty cycles.
Maintenance Focus:
- Oil Management:Replace synthetic oil every 4,000–8,000 hours to prevent friction, reduce energy consumption, and prolong compressor life.Change oil filters every 2,000 hours to avoid clogging and overheating, which can compromise efficiency.
- Separator Efficiency:Inspect the oil-air separator every 3,000–6,000 hours. A failing separator can lead to higher oil consumption and contamination of downstream equipment.
- Cooling System:Clean air/oil coolers annually to maintain optimal thermal efficiency and avoid performance loss due to dust buildup.
Advantages:
- Lower upfront costs compared to oil-free models.
- Robust performance in harsh environments.
- Easier repair and maintenance due to widespread serviceability.
Core Features:
- These compressors provide 100% oil-free air, typically using dry screws or water-injected designs, which are critical for industries requiring clean and dry air.
- Often paired with variable speed drives (VSDs) to enhance energy savings.
Maintenance Focus:
- Air Filtration:Clean intake filters every 1,500 hours to prevent particulate damage to rotors.Replace downstream filters (such as activated carbon) annually to maintain air quality and ensure compliance with ISO 8573-1 Class 0 air purity standards.
- Thermal Monitoring:Regularly monitor discharge temperatures (typically <100°C) to prevent overheating, which can damage the rotors or bearings in oil-free systems.
- Bearing and Gear Care:Inspect and regrease bearings and gears every 8,000 hours to avoid dry friction, which can lead to premature wear.
Advantages:
- Zero risk of oil carryover, making them indispensable for applications where even trace amounts of oil can be detrimental.
- Reduced filtration costs since there is no oil to remove from the compressed air.
- Full compliance with strict air purity regulations in industries like food, pharmaceuticals, and electronics.
Future Trends: Smart, Efficient, and Customizable Solutions
As industries push for greater sustainability and efficiency, screw compressors continue to evolve. Here are a few key trends shaping their future:
- IoT Integration: Advanced Internet of Things (IoT) features allow for predictive maintenance, where real-time monitoring of vibration, temperature, and air flow metrics help prevent failures before they occur, minimizing downtime and repair costs.
- Hybrid Designs: Some manufacturers are now combining the best features of oil-free rotors with energy-efficient VSDs to create hybrid screw compressors. These designs focus on reducing the carbon footprint while maintaining optimal performance.
- Customization: Modular designs enable compressors to be tailored to specific needs, whether for low-flow applications or high-pressure systems, offering unparalleled flexibility for industrial users.
Conclusion: Choosing the Right Compressor for Your Needs
When deciding between oil-injected and oil-free screw compressors, the decision depends on the specific needs of your application:
- Oil-injected screw compressors excel in cost-sensitive, high-load environments where the risk of contamination is minimal.
- Oil-free screw compressors are indispensable in industries requiring high-quality, contaminant-free air—making them a top choice for food, pharmaceutical, and electronics sectors.
As technology continues to bridge the efficiency gap between these two options, innovations in quiet operation, energy savings, and smart maintenance will lead the next era of rotary screw air compressors. Whether your priority is upfront cost or long-term air purity, understanding the unique maintenance demands of each system ensures that you select the best compressor for your needs—maximizing performance, longevity, and energy savings.
By leveraging both oil-free and oil-injected technologies, industries can achieve tailored solutions for a broad range of applications, benefiting from reliable, energy-efficient performance in any environment.