When it comes to air compression, piston compressors—also known as reciprocating air compressors—are among the most widely used types in both industrial and commercial applications. Whether you're operating a small workshop or a large manufacturing facility, understanding how a piston air compressor works can help you choose the right air solutions for your specific needs. In this blog, we'll break down the mechanics of a piston compressor, its key components, and its common applications, including its role in high pressure operations and oil-free designs.
When it comes to air compression, piston compressors—also known as reciprocating air compressors—are among the most widely used types in both industrial and commercial applications. Whether you're operating a small workshop or a large manufacturing facility, understanding how a piston air compressor works can help you choose the right air solutions for your specific needs. In this blog, we'll break down the mechanics of a piston compressor, its key components, and its common applications, including its role in high pressure operations and oil-free designs.
What is a Piston Compressor?
A piston compressor is a positive displacement air compressor that uses the back-and-forth motion of a piston to compress air. The piston moves within a cylinder, and as it travels, it reduces the volume of the air inside the cylinder, increasing the pressure. These compressors are typically categorized into single stage and multi-stage models, with single-stage compressors being most common for lower pressure requirements and multi-stage models used for higher pressure needs.
Reciprocating piston air compressors are ideal for applications that require moderate to high pressure output and are commonly used in industries ranging from construction to automotive repair. They are also found in applications involving natural gas and compressed air systems.
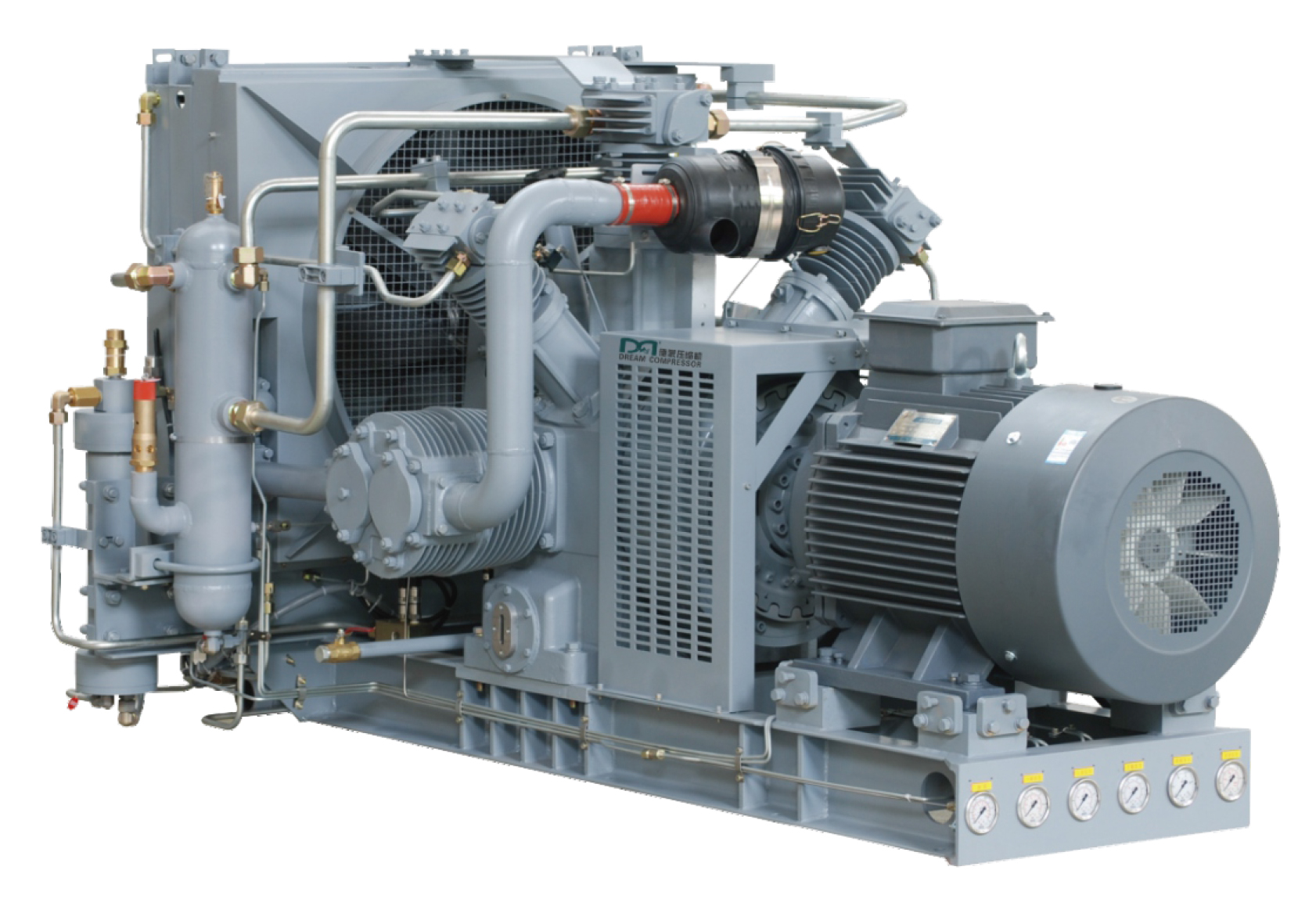
Medium & High Pressure Piston Compressor
How Does a Piston Compressor Work?
The air compressor work process in a piston compressor can be broken down into a few simple steps:
- Intake Stroke: During the intake stroke, the piston moves down the cylinder, creating a vacuum that draws air into the compression chamber through an intake valve. The piston is powered by either an electric motor or a gas engine.
- Compression Stroke: Once the piston has moved to the bottom of the cylinder, it begins its upward journey, compressing the air inside the chamber. As the piston rises, the air's volume decreases, and its pressure increases. The intake valve closes, and the air is sealed within the cylinder.
- Discharge Stroke: As the piston continues to move upward, it forces the compressed air out of the cylinder through a discharge valve. This high-pressure air can be directed into storage tanks, air tools, or other equipment.
- Repeat: This process repeats continuously as long as the compressor is running. The piston’s reciprocating motion—back and forth—is what drives the compression process.
Types of Piston Compressors
There are several types of piston compressors, each designed for specific applications:
- Single-Stage Piston Compressor: In a single-stage compressor, the air is compressed once before being sent out. This type is used in lower pressure applications where the pressure needed is up to about 120 psi (pounds per square inch). These compressors are commonly found in smaller operations and residential applications.
- Two-Stage or Multi-Stage Piston Compressor: In a multi-stage compressor, the air is compressed in stages, with each stage increasing the pressure before it is released. These compressors are more suitable for high-pressure applications and are typically used in heavy-duty industrial environments.
Key Components of a Piston Compressor
- Piston: The piston is the heart of the system, moving back and forth to compress the air within the cylinder. It can be made of durable materials like cast iron, which offers high strength and long-lasting performance.
- Cylinder: The cylinder houses the piston and serves as the chamber where air is drawn in, compressed, and discharged.
- Intake and Exhaust Valves: These valves regulate the intake of air into the cylinder and the exhaust of compressed air. They open and close at precise times to ensure the efficient operation of the compressor.
- Crankshaft: The crankshaft converts the rotary motion of the motor into the back-and-forth motion (reciprocation) of the piston.
- Flywheel: The flywheel helps maintain smooth operation by balancing the forces generated by the piston and reducing vibration.
Advantages of Piston Compressors
- High Pressure: Piston compressors can generate significant high pressure, making them ideal for applications requiring compressed air at pressures greater than what standard rotary compressors can handle.
- Versatility: Whether it’s a single stage or multi-stage compressor, reciprocating piston air compressors can be customized to meet a wide range of industrial needs, including high-pressure systems, oil-free operation, and more.
- Durability: Piston compressors, especially those made with cast iron components, are known for their high quality and long-lasting performance, even under tough conditions.
- Cost-Effectiveness: While not as energy-efficient as some newer compressor technologies, piston compressors are still relatively affordable and easy to maintain, especially for small to medium-sized operations.
An important consideration when choosing a piston compressor is whether to go for an oil-free model or an oil-lubricated model. Oil-free piston compressors are ideal for applications where air quality is paramount, such as in the food and beverage industry or any setting where contamination is a concern. These compressors eliminate the need for oil, meaning the air that exits the compressor is free from oil particles, ensuring clean compressed air.
On the other hand, oil-lubricated piston compressors are typically more durable and can handle more demanding tasks, but they do require regular oil changes and maintenance to keep the system running efficiently.
Industry Applications of Piston Compressors
Piston compressors are widely used across a variety of industries, thanks to their adaptability and performance. Some common industry applications include:
- Construction: Piston compressors are used for powering pneumatic tools, such as drills, hammers, and sanders.
- Automotive: These compressors are essential for car repair shops, where they are used for powering tools like spray guns, impact wrenches, and tire changers.
- Manufacturing: In manufacturing plants, piston compressors provide compressed air for various processes, such as operating machinery, cleaning, and packaging.
- Natural Gas: Piston compressors are also used in the natural gas industry for gas compression, helping to increase the pressure of natural gas for transport.
Noise Levels of Piston Compressors
One downside to piston compressors is their noise levels. Due to their reciprocating action and mechanical components, these compressors can be quite loud. In environments where noise reduction is important, such as in offices or residential areas, oil-free piston compressors might be preferred, as they tend to operate more quietly than oil-lubricated models.
Conclusion
Piston air compressors are a staple in a variety of industries due to their reliability, high pressure capabilities, and versatile design. Whether you're using a single-stage reciprocating piston air compressor for light-duty tasks or a multi-stage compressor for heavy-duty operations, understanding how these compressors work is crucial to selecting the right equipment for your needs. Their oil-free variants provide clean, high-quality compressed air for sensitive applications, while their oil-lubricated counterparts are often more durable and cost-effective for less sensitive environments.
By understanding the key components, functions, and benefits of piston compressors, you can make an informed choice to ensure optimal performance and efficiency in your operations.